Production of
Promobot robots
Promobot headquarters are located in Perm, Russia at «Morion Digital», the largest private technology park in the country. Here, robots undergo the full production cycle: from development and assemblance to testing and sending out.
0
parts per each robot
0
days to finish the production cycle. Every Promobot robot is manufactured manually
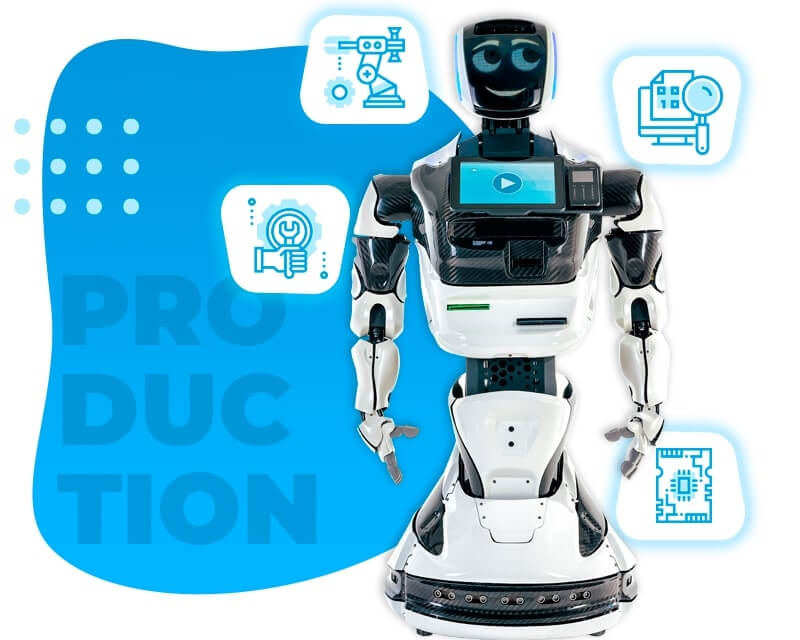
Stages of production
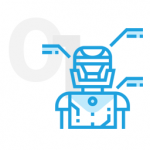
Robot carcass
Promobot carcass is made of lightweight aluminum alloy, moving parts are made of steel
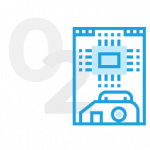
Electronic parts
Wiring, circuit board and processor installment, electronic parts arrangement, servos installment happens at this stage. Special hardware is also being installed during this stage: printers, scanners, bank terminals, etc. At this stage the robot ‘comes to life’ first: after wiring and circuit board installment, robot is being plugged in for the first time at this stage.
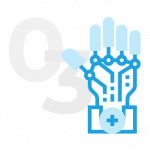
Body
Each plastic part of Promobot’s body undergoes vacuum forming. Afterwards, the parts are painted and being installed on its carcass. Each plastic part of Promobot is fireproof. Promobot V.4 has 56 plastic parts installed ― our clients can select a customized color for them.
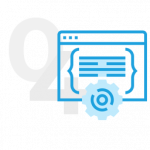
Software
Promobot’s interface is Linux OS by default. At this stage our programmers and linguists develop robot’s linguistic database, face and speech recognition systems, navigation, integrate Promobot with third-party systems (i.e. access control systems, software)
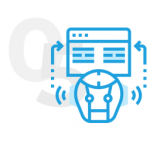
Testing
Each Promobot robot undergoes more than 10 hours of tests during which our engineers troubleshoot and fix any issues until the robot works perfectly
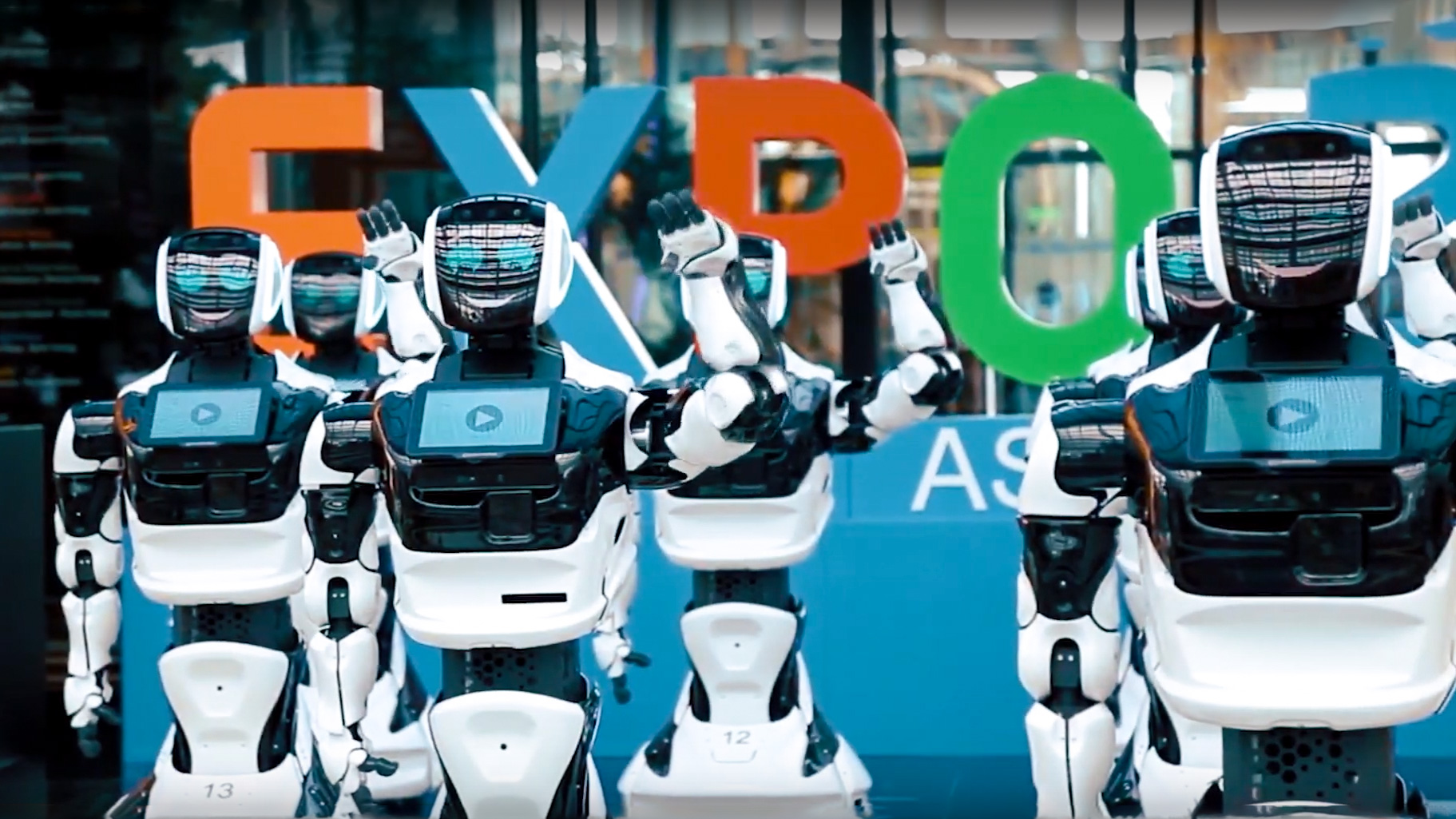